Introduction
The manufacturing sector is currently facing a significant labor shortage crisis, which is one of the major challenges in manufacturing today. This shortage is driven by a combination of factors, including an aging workforce, a widening skills gap, and the lingering effects of the COVID-19 pandemic.
Addressing these labor shortages is crucial for the success of manufacturing businesses. Without sufficient skilled labor, manufacturers struggle with decreased productivity, increased operational costs, and difficulties in meeting production and delivery schedules.
The purpose of this blog is to provide practical strategies to navigate and mitigate labor shortages, one of the biggest HR challenges in the manufacturing sector. By implementing these strategies, manufacturers can improve their ability to attract and retain talent, enhance productivity, and ensure long-term success.
Understanding the Causes of Labor Shortages
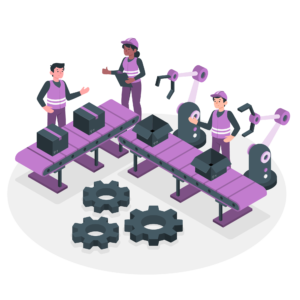
Demographic Shifts and Aging Workforce The manufacturing sector is experiencing a demographic shift as a significant portion of the workforce approaches retirement age. This aging workforce results in a loss of experienced and skilled workers, creating gaps that are difficult to fill with younger, less experienced workers.
Skills Gap and Lack of Qualified Workers Another one of the main challenges in manufacturing is the notable skills gap. Advances in technology and automation require a workforce with specialized skills and training. However, many potential workers lack the necessary qualifications and expertise, leading to a shortage of suitable candidates for manufacturing roles.
Impact of Economic Factors Economic factors such as low unemployment rates and competition from other sectors further exacerbate challenges in manufacturing. With more job opportunities available, potential workers are often attracted to industries that offer higher wages, better working conditions, or more perceived stability, leaving manufacturing roles unfilled.
Effects of the COVID-19 Pandemic on Labor Availability The COVID-19 pandemic has had a profound impact on labor availability. Many workers left the workforce due to health concerns, early retirement, or a shift in career priorities. Additionally, disruptions in education and training programs have slowed the influx of new, qualified workers into the manufacturing sector.
Impact of Labor Shortages on Manufacturing
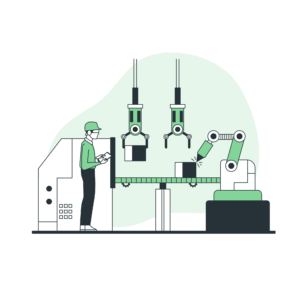
Decreased Productivity and Efficiency Labor shortages lead to decreased productivity and efficiency as manufacturers struggle to maintain their output levels with fewer workers. This often results in longer production times and increased downtime, ultimately affecting the overall performance of the business.
Increased Operational Costs To combat labor shortages and other challenges in manufacturing, companies may need to offer higher wages, better benefits, and invest in overtime pay, all of which contribute to increased operational costs. Additionally, the reliance on temporary or less experienced workers can lead to inefficiencies and increased error rates, further driving up costs.
Delays in Production and Delivery Schedules With fewer workers available, production timelines can be significantly extended. This not only affects the ability to meet customer demands but also disrupts delivery schedules, leading to dissatisfaction and potential loss of clients. Consistent delays can harm a manufacturer’s reputation and competitive edge in the market.
Challenges in Maintaining Quality and Consistency Labor shortages can impact the quality and consistency of manufactured products. Experienced workers are often key to maintaining high standards and ensuring that products meet specific quality requirements. Without them, the risk of defects and inconsistencies increases, which can lead to returns, recalls, and damage to the brand’s reputation.
Severity of the Issue The severity of this issue is highlighted by a report from Deloitte and The Manufacturing Institute, which projects that the U.S. manufacturing sector will have 2.1 million unfilled jobs by 2030 due to labor shortages and skills gaps.
Strategies for Overcoming Challenges in Manufacturing

Attracting and Retaining Talent
- Competitive Compensation and Benefits Packages
- Offering attractive salaries and comprehensive benefits packages can help attract top talent. This includes not only competitive base pay but also health insurance, retirement plans, bonuses, and other financial incentives that make the job offer more appealing.
- Benefits such as tuition reimbursement, paid time off, and flexible spending accounts can further enhance the attractiveness of the compensation package.
- Creating a Positive Workplace Culture
- Cultivating a positive, inclusive, and supportive workplace culture is essential. Employees are more likely to stay with a company where they feel valued and respected.
- Promoting open communication, recognizing employee achievements, and fostering teamwork are critical components of a positive workplace culture.
- Implementing policies that promote diversity, equity, and inclusion can also enhance the workplace environment and attract a wider range of talent.
- Offering Career Development and Advancement Opportunities
- Providing clear pathways for career growth and advancement can motivate employees to stay with the company. This includes training programs, mentorship opportunities, and regular performance reviews.
- Encouraging employees to pursue further education and certifications relevant to their roles can also foster loyalty and engagement.
- Developing leadership programs to prepare employees for management roles can help retain top talent and ensure a strong leadership pipeline within the organization.
Enhancing Training and Development
- Investing in Apprenticeships and Internships
- Apprenticeships and internships can help bridge the skills gap by providing hands-on experience and training to new workers. These programs allow individuals to gain practical skills while earning a salary or stipend.
- Establishing partnerships with local high schools, vocational schools, and community colleges can create a steady stream of apprentices and interns who are eager to learn and contribute.
- Partnering with Educational Institutions for Workforce Training Programs
- Collaborating with local colleges, universities, and trade schools can create a pipeline of qualified workers trained in the specific skills needed for the manufacturing sector.
- Co-developing curricula with educational institutions to ensure that training programs align with industry needs and standards can be particularly effective.
- Providing scholarships, grants, and other financial support to students in relevant fields can also help attract future employees to the manufacturing sector.
- Implementing Continuous Learning and Upskilling Initiatives
- Offering ongoing training and professional development opportunities ensures that employees can continuously improve their skills and adapt to new technologies and processes.
- Online courses, workshops, and seminars can be effective ways to deliver continuous learning programs.
- Encouraging cross-training, where employees learn multiple roles within the company, can enhance workforce flexibility and resilience.
Leveraging Technology and Automation
- Utilizing Robotics and Automation to Supplement the Workforce
- Implementing robotics and automated systems can help alleviate the pressure caused by labor shortages by taking over repetitive and labor-intensive tasks.
- Automation can improve efficiency, reduce errors, and allow human workers to focus on more complex and value-added activities.
- Conducting a thorough analysis of production processes to identify areas where automation can be effectively integrated is crucial for maximizing the benefits of this approach.
- Implementing Advanced Manufacturing Technologies (e.g., AI, IoT)
- Advanced technologies such as artificial intelligence and the Internet of Things can optimize production processes, improve efficiency, and reduce the reliance on human labor.
- AI can be used for predictive maintenance, quality control, and supply chain optimization, while IoT devices can enhance real-time monitoring and data collection.
- Investing in these technologies can lead to long-term cost savings and increased competitiveness in the market.
- Streamlining Operations Through Digital Transformation
- Digital transformation initiatives can enhance overall operational efficiency, reduce waste, and improve communication and collaboration within the organization.
- Implementing enterprise resource planning (ERP) systems, digital twins, and other digital tools can provide better visibility and control over manufacturing processes.
- Embracing digital transformation can also facilitate remote work and flexible scheduling options, making the company more attractive to potential employees.
Improving Recruitment and Hiring Practices
- Expanding Recruitment Efforts to Underrepresented Groups
- Broadening recruitment efforts to include underrepresented groups can help tap into a larger pool of potential workers and promote diversity within the workforce.
- Partnering with community organizations, attending job fairs, and using inclusive language in job postings can attract a more diverse range of candidates.
- Offering support for relocation, childcare, and other barriers that may prevent underrepresented groups from applying can further enhance recruitment efforts.
- Utilizing Data-Driven Recruitment Strategies
- Leveraging data and analytics can optimize recruitment processes, identify the most effective channels for finding talent, and streamline hiring practices.
- Analyzing recruitment data can help identify trends, bottlenecks, and areas for improvement in the hiring process.
- Using applicant tracking systems (ATS) and other recruitment technologies can automate and improve the efficiency of candidate sourcing, screening, and selection.
- Offering Flexible Work Arrangements and Remote Work Options
- Providing flexible work arrangements, such as remote work options and flexible schedules, can make manufacturing roles more attractive to a wider range of candidates.
- Implementing shift-swapping systems, compressed workweeks, and part-time opportunities can also increase job appeal and employee satisfaction.
- Ensuring that flexible work arrangements are supported by appropriate policies, technology, and management practices is essential for their success.
Enhancing Employee Engagement and Satisfaction
- Fostering a Collaborative and Inclusive Work Environment
- Creating a work environment that promotes collaboration, inclusivity, and teamwork can improve employee morale and job satisfaction.
- Encouraging employee input, involving staff in decision-making processes, and providing opportunities for team-building activities can strengthen the sense of community within the workplace.
- Addressing workplace conflicts promptly and effectively, and promoting a culture of respect and inclusion, can further enhance the work environment.
- Implementing Employee Recognition and Reward Programs
- Recognizing and rewarding employees for their hard work and achievements can boost morale and increase retention rates.
- Implementing formal recognition programs, such as employee of the month awards, performance bonuses, and public acknowledgments, can motivate employees to perform their best.
- Providing informal recognition, such as verbal praise, thank-you notes, and team celebrations, can also contribute to a positive work culture.
- Providing Support for Work-Life Balance and Mental Health
- Offering resources and support for work-life balance, such as mental health services, flexible schedules, and wellness programs, can help employees manage stress and maintain a healthy work-life balance.
- Providing access to counseling, stress management workshops, and wellness initiatives can improve overall employee well-being.
- Encouraging employees to take regular breaks, use their vacation time, and engage in activities that promote physical and mental health can lead to a more productive and satisfied workforce.
Enhancing Employee Engagement and Satisfaction
- Fostering a Collaborative and Inclusive Work Environment
- Creating a work environment that promotes collaboration, inclusivity, and teamwork can improve employee morale and job satisfaction.
- Implementing Employee Recognition and Reward Programs
- Recognizing and rewarding employees for their hard work and achievements can boost morale and increase retention rates.
- Providing Support for Work-Life Balance and Mental Health
- Offering resources and support for work-life balance, such as mental health services, flexible schedules, and wellness programs, can help employees manage stress and maintain a healthy work-life balance.
General Best Practices and Recommendations
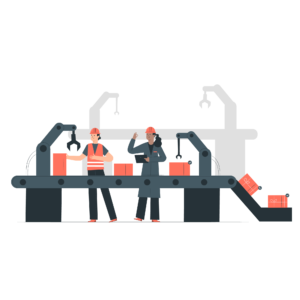
Summary of Best Practices That Can Be Applied Across the Manufacturing Industry
- One of the most important practices is to foster a positive workplace culture as you battle challenges in manufacturing. Cultivating an environment of respect, inclusion, and collaboration helps retain employees and attract new talent.
- Investing in employee development is crucial. Providing ongoing training and development opportunities keeps your workforce skilled and adaptable.
- Leveraging technology, such as automation, AI, and IoT, streamlines processes and reduces dependency on human labor.
- Offering competitive compensation packages ensures your offerings are attractive within the industry.
- Implementing flexible work arrangements, such as remote work options and flexible schedules, meets the diverse needs of employees.
- Enhancing recruitment strategies by using data-driven methods and expanding efforts to reach underrepresented groups is beneficial.
- Prioritizing employee well-being by providing resources for mental health, work-life balance, and overall wellness can greatly improve job satisfaction and retention.
Tips for Customizing Strategies to Fit Specific Organizational Needs
- Assess your workforce needs regularly to understand the specific skills and roles required within your organization.
- Tailor training programs to address the unique skills gaps and developmental needs of your workforce.
- Adjust compensation packages to benchmark against industry standards and attract top talent.
- Choose technology solutions that align with your specific operational requirements and budget constraints.
- Implement flexible work arrangements that suit the nature of your operations and employee preferences.
- Develop personalized employee engagement strategies based on feedback and the unique culture of your organization.
Emphasizing the Importance of a Proactive and Flexible Approach
- Be proactive by anticipating potential labor shortages and taking early action to address them.
- Stay flexible and be willing to adapt strategies and approaches as the labor market and organizational needs evolve.
- Maintain open lines of communication with employees to understand their needs and concerns.
Conclusion
In this blog, we discussed the significant labor shortages challenging the manufacturing sector and explored strategies like attracting and retaining talent, enhancing training, leveraging technology, improving recruitment, and boosting employee engagement.
Key points included fostering a positive workplace culture, investing in continuous learning, utilizing advanced technologies, and offering competitive compensation and flexible work arrangements. We emphasized personalized approaches and proactive measures to effectively address labor shortages.
Manufacturers must adopt these strategies to ensure sustained success in an evolving industry. By being proactive, flexible, and committed to continuous improvement, they can overcome labor shortages and achieve long-term growth and productivity.
Consider using Woliba to help employees prioritize their well-being. Woliba offers wellness programs and resources that enhance employee satisfaction and engagement, contributing to the success of your manufacturing operations.